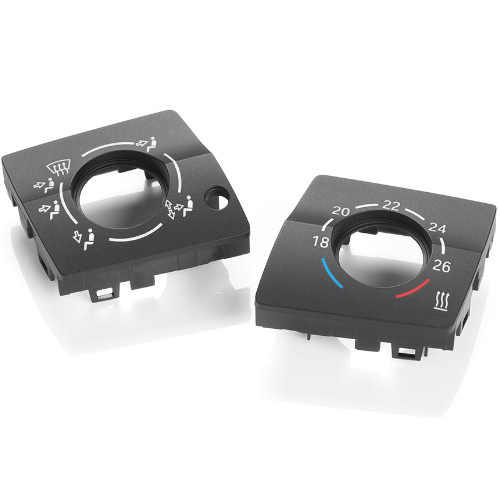
Laser marking is characterized by several advantages over other marking processes, whether as an integration system in production lines, production lines or as a manual workstation. Laser marking is a process that generally requires no mechanical intervention. As the tool is a massless laser beam that only works with wavelengths, there is no need to clamp the semi-finished product to be marked, which in turn significantly reduces set-up times.
Another advantage of laser marking is that, as a rule, no auxiliary and operating materials are required, which keeps both maintenance costs and investment costs low in the short and long term. With laser marking, only the material properties are changed, so that all types of marking or lettering are activated from the properties of the material, such as metal, wood or aluminum.
In addition, laser markers are largely wear-free means of production. Little mechanical work is required, which reduces the susceptibility to faults and therefore the maintenance intervals of the laser markers.
Finally, this marking process is characterized by its high flexibility. Information can be changed very quickly using laser marking software and output immediately on the material to be marked. Whereas in the past it was necessary to produce complex matrices with corresponding contours, today any contour can be scanned with the laser beam.
Annealing marking is a special method of laser marking for metals. The heat of the laser beam creates an oxidation process under the surface that changes the color of the metal. This precise and permanent marking is ideal for industrial applications such as serial numbers and logos.
During laser marking, the heat of the laser beam triggers a chemical reaction in the material, which leads to a change in color. Depending on the composition of the material, different shades of color are created. For example, soot can be produced when marking light-colored plastic, resulting in a dark marking.
Laser engraving is a method in which the surface of a material is melted and vaporized by a laser beam. This removes material, creating an indentation known as an engraving. This method enables precise and permanent markings to be made on various materials.
Laser ablation involves the targeted removal of top layers of materials to create a clear contrast with the layer underneath. This technique uses the precision of the laser beam to remove the top layer, leaving a clear mark. Typical applications include anodized aluminium, painted metals, foils and laminates.
Foaming is a method in which the laser beam heats and melts the material. This creates tiny gas bubbles inside the material, which scatter the light and create a bright marking. This technique is used particularly with dark plastics to achieve highly visible and high-contrast markings.
Carbonization is a special method of laser marking that creates impressive contrasts, especially on light-coloured surfaces. The surface of the material is heated to at least 100°C by the laser. This heat leads to the formation of gases such as oxygen and hydrogen, resulting in a darker layer with a higher carbon content. This process is ideal for materials such as polymers, wood and leather. However, as carbonization creates dark markings, the contrast on dark surfaces is less pronounced.
Press ENTER to confirm or press ESC to close